5 Things You Need to Include in a Warehouse Safety Checklist
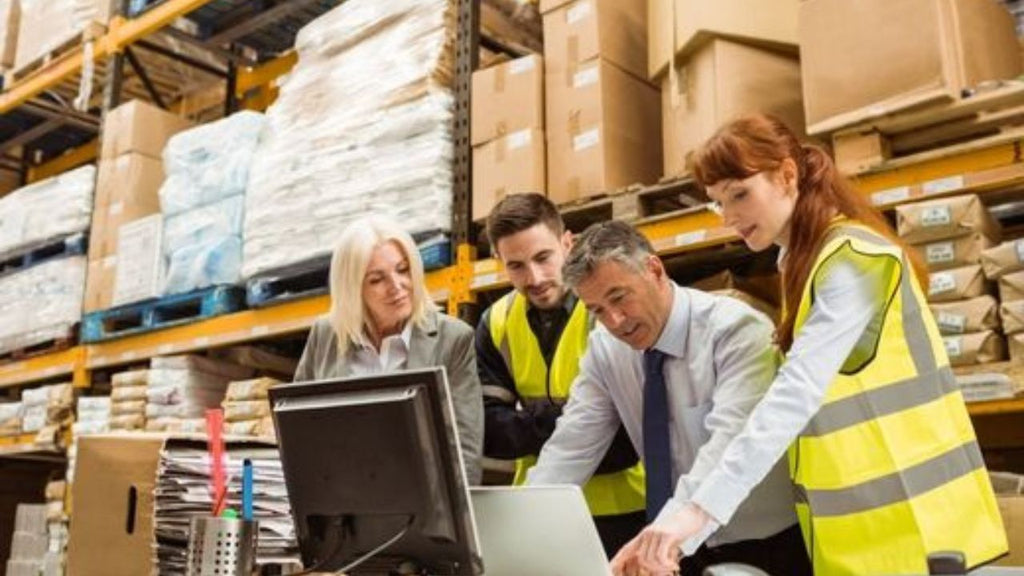
Warehouses aren't getting any safer. More than 250,000 workers in the transportation and warehousing sectors were injured or sick due to workplace accidents in 2021. That's up by nearly 50,000 injuries since 2020.
Creating a safe work environment is essential for all warehouse supervisors. If you're struggling to create a safe warehouse, you should develop a warehouse safety checklist to make things easier. Your list must have a few essential items.
What safety resources should you have in your warehouse environment? What regulations should you start following? When and how should you inspect your warehouse?
Answer these questions and you can create a perfect warehouse environment in no time. Here are five things that must go on your safety checklist.
1. Hanging up Emergency Signs
OSHA standard 1910.37 requires you to maintain exit routes so there is no significant danger to employees. Signs are critical components of exit routes, and each exit must be marked with a sign that reads "Exit." The letters in "Exit" must be six inches tall.
If the direction of travel to the exit is not clear, you must post signs showing where people should go. You also must put up signs that read "not an exit" if someone may mistake a door for an emergency exit.
Each sign should be illuminated and distinct in color. Many signs are red because red is easy to see from a distance, but you can make your signs orange or yellow as well. Consider buying signs that are battery-powered so they will remain on after a power outage.
In addition to exit signs, you should buy and maintain additional signs. Danger signs are used in areas where immediate hazards like falling objects exist. They are in red, and they should be as visible as your exit signs.
Caution signs designate areas where potential hazards like toxic materials are present. These signs are yellow, and they can include text that informs workers about the dangers.
2. Checking Storage Racks
Storage racks prevent spills and allow for easy organization of your hazardous materials. You should inspect your racks multiple times a week for signs of damage like bent materials and holes. You must repair your racks as soon as you notice problems.
Place labels and signs on each rack so your employees know where items go. Make sure the aisles are big enough to accommodate bulky machines and large groups of employees walking together.
Be careful with how you store items on your racks as well. The height of stacked items should not be so high that they can topple over. Racks should be spaced apart so items on one rack do not touch the bottom of another rack.
3. Inspecting the Ventilation System
When people think about warehouse safety, they often think about heavy equipment and hazardous materials. But your workers can get injured by breathing in particulates and unclean air.
You and a ventilation professional should inspect the ventilation system at least once a week. If you work with particulates and pathogens, you may need to inspect the system more frequently.
The filters in your system catch particulates and debris like hair. If your filters get clogged, your air quality will go down, and very little air may pass through your ventilation system. You should replace your filters multiple times a month with identical versions of your old filters.
You can open doors and windows to improve the ventilation in your warehouse. But make sure that debris or wind cannot interfere with your operations. You can install screens over your doors and windows to prevent this, though you should inspect them to make sure they are not tattered.
4. Wearing Safety Equipment
All employees and guests in your warehouse should wear warehouse safety equipment. Everyone must wear a reflective vest that is visible from a distance.
The vest can be any color, though yellow reflective strips on red or orange fabric can be easy to see. If visibility is low in your warehouse, your employees can wear high-visibility pants and sweatshirts.
If falling objects are a hazard, your employees should wear hard hats. The hats should fit over the top of their head, and chin straps can be used to keep them in place. Workers should also wear eye goggles and respirators when they are cutting items or transporting particulates that can land in their eyes or mouths.
5. Examining Heavy Machinery
You should inspect each piece of machinery at the start and end of the work day. Take photographs and written notes on any differences you notice between your inspections.
Look at the owner's manual for your machinery. Manufacturers give clear instructions on how you should inspect their products. The manual may also let you know when components are expected to break down, letting you order preventative maintenance.
Start by examining the safety components of the machinery. Test the brakes, seat belts, and parking system. Do a test drive in the loading bay and see if the machine can be steered and accelerated properly.
You should inspect the machine for any signs of damage or wear. Look at the tires and frame before checking the fluid levels. If everything seems fine, you can prepare the equipment for operation by greasing it.
Developing a Warehouse Safety Checklist
A warehouse safety checklist is a necessary tool for all warehouse supervisors. You should hang up emergency signs near exits and exit routes. You should also check storage racks and ventilation equipment for signs of damage and make fixes right away.
All employees should wear safety equipment like reflective vests and hard hats. At the start and end of each day, you need to look at your machinery and vehicles and make sure they work perfectly.
Create your safe warehouse with the best safety tools. Hi-Viz.com provides the best high-visibility clothing on the market. Browse our store today.